Kiedy początku ubiegłego roku firma Kiewit-Bilfinger Berger JV przystępowała do wykonania instalacji mikrotunelowych nr 4 i 5 wchodzących w zakres projektu East Side CSO Tunel, inżynier kontraktu JV Parsons Brinckerhoff, i urząd odpowiedzialny za środowisko w Portland (Bureau of Environmental Services (BES)) zdecydowały się na eliminację pośredniego szybu technologicznego. W wyniku tej decyzji dwa odcinki o długościach odpowiednio 589 m i 302 m zostały zamienione pojedynczy przecisk o niebagatelnej długości ponad 900 m (3000 stóp). Wcześniejsza rekordowa mikrotunelowa instalacja w Ameryce Północnej miała długość 495 m i została wykonana 18 lat temu na wyspie Staten przez E.E. Cruz & Co. of Holmdel, N.J.
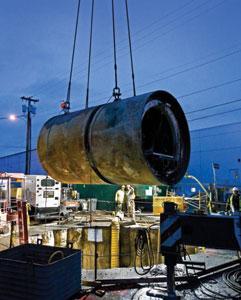
Portland jest najbardziej deszczowym miastem w USA i występuje tam o wiele więcej opadów, niż byłoby to konieczne. Deszcz pada intensywnie przez 100 dni w roku, co powoduje przepełnianie kolektorów kanalizacyjnych. Kiedy pojemność kanału ściekowego jest przekroczona, nieczystości wpływają do rzeki Willamette, dopływu rzeki Columbia. Dlatego powstał program East Side Combined Sewer Outflow, będący częścią ogromnego przedsięwzięcia mającego na celu eliminowanie przedostawania się ścieków do rzeki.
Jedną z części projektu było West Side CSO, w ramach którego wykonane zostało w 2005 roku tunelowanie na dystansie blisko 6 km, a instalacja została podłączona w 2006 r. Kiedy program East Side CSO zostanie zakończony w 2011 r., przepływ ścieków z kanału do rzeki Willamette zostanie zredukowany o 94%.
Kontrakt Kiewit-Bilfinger Berger JV (KBB) na wykonanie projektu East Side opiewa na 381 milionów USD, a w jego zakresie ma powstać tunelowa instalacja o długości 9,6 km i średnicy 6,7 m, ułożona na głębokości od 26 m do 50 m pod powierzchnią. Ponadto powstało siedem szybów roboczych, ponad 1800 m mikrotunelu i blisko 1000 m instalacji układanej w otwartym wykopie. Część mikrotunelowa projektu została podzielona na kilka odcinków o różnych długościach. Odcinek łączący Outfall 46 i Port Center Way został zaprojektowany przez Parsons Brinckerhoff jako mikrotunel w dwóch odcinkach. Kiedy JV zasugerował taką kombinację instalacji, BES musiał rozważyć kwestię potencjalnych „za” i „przeciw” wynikających z dłuższych instalacji. „Ten kontrakt budowlany jest tak skonstruowany, że praca, wyposażenie i wykorzystane materiały mają się zwrócić inwestorowi”, wyjaśnia Paul T. Gribbon, P.E., główny inżynier projektu tunelowego Willamette River CSO. „BES wkalkulowało ryzyko w projekt poprzez akceptację ryzykownie długiej instalacji w trudnych warunkach gruntowych bez względu na potencjalne oszczędności wynikające z eliminacji szybu pośredniego. Decyzja o podjęciu tego ryzyka wynikała z wcześniejszego doświadczenia w mikrotunelowaniu w podobnych warunkach i przy użyciu podobnej maszyny w ramach projektu West Side CSO”.
Ostatecznie decyzja ta była wspólnym ryzykiem powziętym zarówno przez inwestora, projektanta i wykonawcę. Zadanie było mało prawdopodobne do wykonania, jeśli w ogóle możliwe przy takiej ofercie przetargowej.
Instalacja
Firmie Herrenknecht nie jest obce ustanawianie rekordów w instalacjach mikrotunelowych. Zgodnie z tym, co mówi Julian O ’ Connell, konsultant ds. sprzedaży i spraw technicznych w Herrenknecht, najdłuższą wykonaną w technologii mikrotunelu instalacją była ta o długości 2600 m, wykonana przy użyciu maszyny Herrenknecht. Instalację tę wykonano w Niemczech, co ma znaczenie, bo inaczej mikrotunelowanie jest definiowane w warunkach europejskich a inaczej w Ameryce Północnej.
Mikrotunelowanie w Ameryce Północnej jest opisane jako proces, w którego instalowany jest rurociąg, podczas gdy w Europie odnosi się do rurociągów o danym rozmiarze. Innymi słowy, europejskie mikrotunele są małymi tunelami (zasadniczo odnosi się to do średnic od 914 mm (36 in.) do 1219 mm (48 in.)). W Ameryce Północnej mikrotunelowanie jest procesem, w którym wykorzystuje się zdalnie sterowane urządzenie wiertnicze. Bez względu na średnicę, jeśli maszyna jest zdalnie operowana (kierowana) wpisuje się w północnoamerykańską definicję mikrotulelowania.
Długość typowego północnoamerykańskiego mikrotunelu liczona jest raczej w setkach niż w tysiącach stóp. Ta szczególna instalacja już w swojej oryginalnej specyfikacji byłaby rekordowa, ale po zwiększeniu jej długości o połowę stała się ona jeszcze większym wyzwaniem. Zgodnie z tym, co powiedzieli Scott Wimmer, menadżer w zakresie mikrotunelowania z KBB i wiertniczy superintendent Matt Roberts, grunt w jakim pracowała maszyna na odcinku nr 4, jest w przeważającej większości złożony z piasku, mułu i osadów rzecznych. Odcinki od 1 do 3 były instalowane w miejscu, gdzie formacja składała się z drobnego materiału aluwialnego ze znaczącą zawartością żwiru i kamieni.
“Przy pierwszych instalacjach nie było zbyt wielu niespodzianek”, powiedział Wimmer. „Napotkaliśmy jedynie trochę drewnianych przeszkód, ale maszyna MTBM dobrze sobie z nimi poradziła”. „Zastosowaliśmy także wirówkę dekantacyjną dla poprawy efektywności separacji drobnej fazy stałej, takiej jak pył i ił” - dodał Roberts. „Dostęp do powierzchni nad tunelem jest bardzo ograniczony”, mówi Kiewit’s Bill Mariucci. „Dodać do tego należy fakt, że instalacja przebiegała równolegle do torów kolejowych”.
Ponieważ linia wiercenia przebiegała blisko rzeki, proces narażony był na bezpośredni wpływ wody gruntowej. „Przewidzieliśmy że mikrotunelowanie w takich warunkach będzie wyzwaniem też z tego powodu, że w obszarze prac przeciskowych znajdowało się sporo fragmentów pali drewnianych i odpadów przemysłowych”, mówi Roy Cook, menadżer projektu z Parsons Brinckerhoff. „Ten rekord to prawdziwe osiągnięcie załogi obsługującej maszynę mikrotunelową i inspektorów budowlanych, którzy utrzymali ścisłą kontrolę nad przebiegiem prac”.
Urządzenie
Maszyna MTBM wykorzystana w projekcie to model AVND2000 firmy Herrenknecht, wyposażona w głowicę skrawającą o średnicy 2654 mm. Główną cechą tej maszyny jest to, że umożliwia zastosowanie zmiennych trybów przepływu płuczki sprawdzających się w różnych warunkach gruntowych. Urządzenie wyposażone jest w bardzo wydajną kruszarkę i posiada łatwy dostęp do głowicy, w celu wymiany części tnących. Dodatkowe udogodnienia i regulacje poczyniono w zakresie oświetlenia na całej długości wykonywanej instalacji.
„Urządzenie elektryczne zostało zamontowane na łatwo poruszającej się przesuwnej platformie, tak by łatwo dało się przemieszczać na całej długości tunelu”, wyjaśnia O’Connell. „Co więcej, zainstalowany został też system żyroskopowy służący do sterowania” Zaznaczył, że długość odcinka znajduje się poza zasięgiem zwykłego nawigacyjnego systemu typu laserowego. Inną cechą, która dostosowuje tę maszynę do dłuższych odcinków jest to, że dostęp do przodka możliwy jest przez drzwi. Kontrolowanie tarczy skrawającej i wymiana ostrzy mogą odbywać się przez komorę ciśnieniową. „Oczywiście narzędzia tnące się zużywają, po pewnym czasie postęp maleje, a długość pojedynczego odcinka jest swoistym kompromisem”, mówi O’Connell.
Proces drążenia
„Innym głównym czynnikiem sprzyjającym odniesieniu sukcesu jest właściwe wykorzystanie kilku pośrednich stacji siłowników”, zaznaczył Wimmer. Stacja pośrednia (IJS - intermediate jacking station) to stalowy cylinder wyposażony w hydrauliczne siłowniki zamontowane między dwoma segmentami rur w rurociągu w celu równomiernego przenoszenia nacisku (sił osiowych) na całej długości instalacji. Siedem pośrednich stacji o sile pchania 1100 T zostało wykorzystanych do wykonania instalacji, przy czym pierwsza została zamontowana w odległości około 45 m za głowicą mikrotunelową. Następne stacje były montowane po każdych 128 m tunelu. Siła pchania wzrastała od 150–250 T aż do 700 T przy końcu instalacji.
KBB zastosowało również Automatic Bentonite System firmy Herrenknecht, aby zapewnić odpowiednie smarowanie przestrzeni pierścieniowej pomiędzy gruntem a przeciskaną rurą. Betonowy rury przeciskowe zainstalowane za maszyną MTBM miały średnicę ID 2134 mm. “Kluczem do wykonania instalacji tej długości jest utrzymywanie niskiego współczynnika tarcia i skorelowanych z nim niskich sił przeciskowych” wyjaśnia O’Connell.
W czasie, kiedy trwał proces instalacji, zauważono, że warunki gruntowe były gorsze niż to przewidywano. Pojawiło się sporo drewnianych kawałków pochodzących z doków oraz żelazny złom, który znacznie spowolnił postęp prac. Konieczna była naprawa kilku elementów maszyny i oczyszczenie trasy. Mimo trudności, przezwyciężono je, a MTBM ustanowiła rekord. Wykonanie instalacji zajęło 60 dni roboczych, każdy z dwoma 10 godzinnymi zmianami. Średni dzienny postęp wynosił około 16,5 m, a największy postęp zanotowano w dniu, gdy wykonano ponad 43 m instalacji.
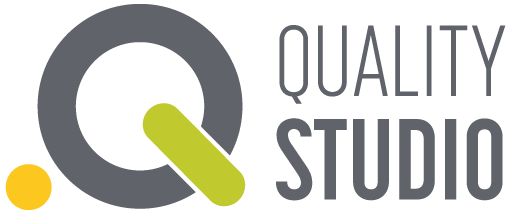
Foto, video, animacje 3D, VR
Twój partner w multimediach.
Sprawdź naszą ofertę!
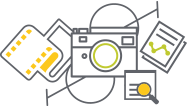
Powiązane
Aby dodać komentarz musisz być zalogowany. Przejdź do formularza logowania/rejestracji.