Korozja metali jest problemem odkąd człowiek zaczął zajmować się wydobyciem, wytapianiem i obróbką metali. Problem ten dotyczył powstawania rdzy na żelaznych narzędziach, broni, hełmach, zbrojach, a także rdzawych nalotach na spiżowych dzwonach lub dachach z miedzi. Starano się wtedy zapobiegać zniszczeniom przez pokrywanie przedmiotów smołą, olejem roślinnym, woskiem lub tłuszczem zwierzęcym. A dzisiaj? W jaki sposób walczy się z problemem korozji?

Ochrona metali przed rdzą
Na przestrzeni dziejów człowiek dokonał odkryć wielu metali i opracował nowe stopy, wśród których znajdują się takie, które są odporne na rdzę. W zależności od tego, jakie właściwości w procesie obróbki są potrzebne, należy zadbać o mniejszą lub większą ochronę przed korozją. Często kosztem większej trwałości lub wytrzymałości jest zmniejszona odporność metalu lub jego stopu na rdzę i należy liczyć się z koniecznością szczególnego zadbania o ochronę metalu. Obecnie można stosować różne techniki zabezpieczeń antykorozyjnych metali i ich stopów. Schemat ochrony jest jednak zawsze podobny i dotyczy pokrycia jednego metalu drugim, który stanowi powłokę ochronną. Najbardziej powszechne są powłoki metalowe, a także te powstałe z niemetalowych substancji nieorganicznych. Powłoki organiczne, takie jak powłoki bitumiczne, smary, lakiery, farby i tworzywa sztuczne są równie popularne. Stopień zagrożenia korozją jest ważną informacją, gdyż na tej podstawie wybiera się odpowiednią powłokę ochronną. Powłoki ochronne dzielimy na anodowe i katodowe, co jest związane z mechanizmem ich działania.
Powłoka ochronna przez cynk
Wykorzystanie cynku jest najbardziej powszechne w tworzeniu powłoki ochronnej dla stali i żeliwa. Powłoki anodowe związane są z zabezpieczeniem metalu szlachetnego przez metale nieszlachetne. Powłoka cynkowa buduje warstwę ochronną, która działa jak anoda chroniąca stal. Proces cynkowania dotyczy przejęcia elektronów, a także przedostania się go do roztworu, gdzie jednocześnie cząsteczki żelaza nie są wypłukiwane. Ochrona zapewniona przez cynk jest wzmacniana przez obecność dwutlenku węgla z powietrza, gdyż w takim środowisku powstaje dodatkowo pasywna warstwa węglanowa, a w środowisku alkaicznym warstwa pasywnego wodorotlenku cynku. Doskonałym obszarem tworzenia powłoki ochronnej przez cynk jest środowisko o pH od 6 do 11. Cały proces związany jest z zanurzeniem w stopionym ogniwie (metalu) lub przez elektrolizę (galwanizację). Często wykorzystywany w tworzeniu tych powłok jest także kadm.
Ochrona przez metale szlachetne
Druga technika ochrony metali związana jest z zabezpieczeniem metali mniej szlachetnych tymi, które są bardziej szlachetne. W tej metodzie popularne jest tworzenie powłok miedziowych, niklowych, chromowych, srebrnych i cynowych. W ten sposób tworzona jest powłoka katodowa, która sprawdzi się tylko wtedy, gdy ochroną objęta jest cała powierzchnia metalu. Uszkodzenie takiej powłoki powoduje przyspieszenie korozji w miejscu pęknięcia, co następuje szybciej niż w przypadku metalu nieposiadającego takiej powłoki. Do popularnej techniki katodowej zaliczyć trzeba miedziowanie. Wysoki potencjał elektrotechniczny, jaki posiada miedź dotyczy jej większej odporności na rdzę niż innych metali konstrukcyjnych, takich jak aluminium, cynk lub żelazo. Miedziowanie realizowane może być elektrolitycznie, w roztworach cyjankowych i siarczanowych. Bezprądowa metoda z kolei ma związek z zanurzaniem w roztwór soli miedzi (II) oraz samoczynnym wytrącaniu się miedzi na powierzchnię metalu. Techniki takiego osadzania, będące ochroną innych metali opracowano także dla kobaltu, palladu, cyny, miedzi, srebra, złota i platyny. Taka ochrona antykorozyjna jest jednak rzadko stosowana.
Pozostałe możliwości ochrony
Poza wymienionymi metodami stosuje się także:
- tworzenie ochronnych powłok cynkowych, cynowych, ołowianych i aluminiowych przez zanurzenie chronionego metalu w stopionym metalu z wymienionych wyżej;
- zabezpieczenie metalu chronionego przez natryskiwanie innym metalem;
- nakładanie sproszkowanego metalu i jego późniejsze wyżarzanie. Dotyczy to zabezpieczeń powstałych przez aluminium oraz chrom;
- platerowanie, czyli mechaniczne pokrycie warstwą metalu.
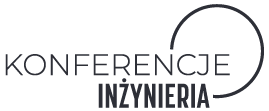
Konferencje Inżynieria
WIEDZA. BIZNES. ATRAKCJE
Sprawdź najbliższe wydarzenia
Aby dodać komentarz musisz być zalogowany. Przejdź do formularza logowania/rejestracji.