Planowana bezwykopowa renowacja rurociągu jest sporym wyzwaniem – kiedy jednak należy taki projekt zrealizować szybko, w obliczu nagłej potrzeby, poziom trudności zadania rośnie. Dlatego sprawna i efektywna modernizacja gazociągu w South Orange (New Jersey, USA), który uległ uszkodzeniu, została doceniona przez jury magazynu „Trenchless Technology”. Jurorzy przyznali inwestycji tytuł Projektu roku w kategorii Renowacja.
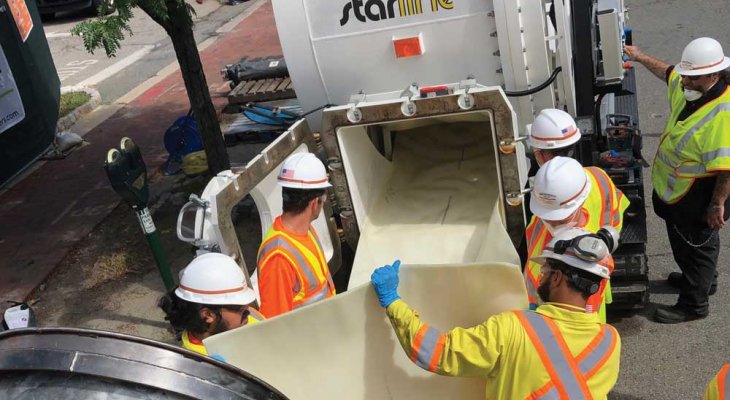
Kiedy inwestor – Public Service Electric and Gas Co. (PSE&G) – zauważył wyciek z magistrali gazowej (w obrębie stalowego reduktora o wymiarach 914 x 762 mm), tymczasowo zlikwidował szkodę, instalując betonowy oczep oraz przewód DN50, mający odprowadzić uciekający gaz.
Dzięki temu zabezpieczeniu uzyskano czas potrzebny na zaprojektowanie renowacji magistrali posadowionej na głębokości ponad 3 m, a poprowadzonej w bliskiej odległości od wielkośrednicowej magistrali wodociągowej, sieci teletechnicznej oraz innych elementów infrastruktury podziemnej. Projektanci musieli uwzględnić także fakt, iż w obrębie krótkiego, bo zaledwie 175-metrowego odcinka, wykonawca będzie musiał pokonać aż sześć łuków. Ogromną trudność sprawił także wyjątkowy „bałagan”: przewód przekraczał rzekę Rahway, a po drugiej jej stronie łączył się z niedostępnym zaworem nieszczelnym reduktorem i krótkim odcinkiem innej rury żeliwnej, przesyłającej paliwo w kierunku zachodnim.
Wykonawca zdecydował się na technologię CIPP, tj. wykładziny utwardzanej na miejscu. Jak twierdzi George Ragula, dyrektor generalny RagulaTech (a jednocześnie inżynier projektu), była to jedna z najbardziej złożonych realizacji CIPP w historii firmy. Ponad 900-milimetrowy rękaw przejść bowiem musiał przez reduktor, rurę 762-milimetrową, zawór, drugi reduktor, by wreszcie dotrzeć do właściwego przewodu. To jednak nie był koniec: w docelowej rurze również montaż był utrudniony z uwagi na trasę poprowadzoną po łuku.
Innowacyjny projekt
Wykonawca zamówił, przetestował i zainstalował nowy zawór, rozbudował odcinek o 10 m z wykorzystaniem nowej rury, a następnie przygotował przewód wprowadzający o rozmiarach niemal identycznych z oryginalnymi rozmiarami magistrali – aby zapewnić prawidłowe umieszczenie wykładziny w rurze. Dzięki temu na powierzchni wykładziny miało nie być nierówności, a cała konstrukcja powinna być strukturalnie prawidłowa.
Zbudowano i przetestowano również tymczasowy korek ograniczający o średnicy 500 mm, który miał zablokować przyłączony do magistrali kanał boczny i w ten sposób zapewnić powierzchnię nośną, gdy wykładzina będzie przechodzić przez kanał boczny.
Przed przystąpieniem do instalacji wykonano także nietypowy dla tego typu projektów zabieg: iniekcję kurtynową, aby zatrzymać napływ wody i infiltrację do rury po obniżeniu ciśnienia w jej wnętrzu.
Dopiero po zakończeniu przygotowań przystąpiono do instalacji wykładziny: ku zdumieniu, ale i radości ekipy, wykonania zadania nie przerwały żadne nieprzewidziane problemy. Udało się przeprowadzić wszystkie prace w założonym czasie.
Po zakończeniu spoinowania, czyszczenia, inspekcji i epoksydowania, wykonawca był gotowy do instalacji rękawa. W sumie, inwersja zajęła mniej niż dwie godziny. W miejscach, gdzie ponad 900-milimetrowa wykładzina marszczyła się, tj. w sekcjach 762-milimetrowych, puste przestrzenie za nierównościami zostały wypełnione żywicami. Dzięki temu gaz nie wydostanie się z rury, nawet jeśli wykładzina okaże się nieszczelna. W ten sposób udało się zabezpieczyć gazociąg, jednocześnie przedłużając jego żywotność o kolejne dekady.
Wdrożyliśmy wiele innowacji i nietypowych rozwiązań – mówi George Ragula. Tylko dzięki temu udało się poprawnie zrealizować projekt... i odnieść sukces.
Więcej na temat tego projektu przeczytać będzie w można w kolejnym numerze kwartalnika „Inżynieria Bezwykopowa”.
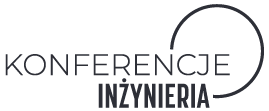
Konferencje Inżynieria
WIEDZA. BIZNES. ATRAKCJE
Sprawdź najbliższe wydarzenia
Aby dodać komentarz musisz być zalogowany. Przejdź do formularza logowania/rejestracji.