Podczas prac wiertniczych warunki geologiczne bywają złożone. O realizacji projektów bezwykopowych w skomplikowanych formacjach żwirowych mówił podczas tegorocznej konferencji „INŻYNIERIA Bezwykopowa” Marcin Firkowski z firmy PPI Chrobok S.A. Na konkretnych przykładach pokazał, jak w takich warunkach sprawdza się technologia Direct Pipe.
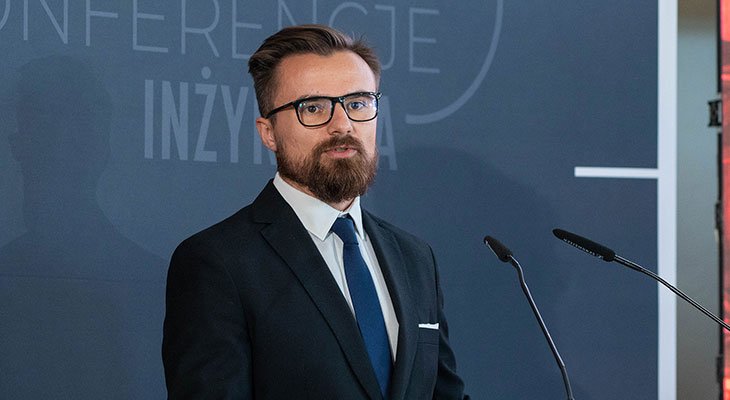
Podczas wystąpienia Marcin Firkowski przedstawił realizację dwóch projektów w technologii Direct Pipe (DP). Pierwszy to wiercenie w Serbii pod rzeką Vielika Morava, a drugi – w okolicach Nowego Targu pod rzeką Białką. W obu przypadkach panowały skomplikowane warunki geologiczne w postaci m.in. żwirów i otoczaków. I właśnie w takich przypadkach sprawdza się DP: ogranicza ryzyko występowania niestabilnego otworu wiertniczego i utrzymuje cyrkulacje płuczki wiertniczej.
Prelegent przypomniał, że na świecie wykonano już 155 instalacji z użyciem technologii Direct Pipe. 19 z nich zrealizowała spółka PPI Chrobok. Najdłuższy rurociąg miał 2220 m, a polska spółka wykonała dotychczas zadanie o długości 700 m. Najwięcej takich projektów realizuje się w Stanach Zjednoczonych i Kanadzie, natomiast w Europie – w Polsce i we Włoszech.
Direct Pipe
Marcin Firkowski, opisując technologię DP, podkreślił, że łączy ona zalety HDD (ang. Horizontal Directional Drilling – horyzontalne wiercenie kierunkowe) i mikrotunelowania. Zapewnia większą efektywność podczas wiercenia w złożonych warunkach gruntowych, zmniejsza plac po stronie wyjściowej oraz ryzyko szczelinowania hydraulicznego, a dodatkowo umożliwia instalowanie rurociągu w sekcjach i podnosi bezpieczeństwo pracy.
DP pozwala też na wykonanie jednoetapowo otworu wiertniczego wraz z ułożeniem rurociągu. Podobnie jak w mikrotunelowaniu urobek jest skrawany przez głowicę mikrotunelową, natomiast trajektorie są podobne do spotykanych w HDD. W DP za pomocą siłowników hydraulicznych można zmieniać kąt nachylenia głowicy wiercącej i w ten sposób zmieniać kierunek wbudowywanego rurociągu. Jego układanie odbywa się pod kontrolą zdalnej nawigacji z żyrokompasem, a urobek jest usuwany poprzez rury płuczkowe ułożone wewnątrz instalowanego rurociągu stalowego. Z kolei rama pchająca Pipe Thruster dostarcza siłę niezbędną do prowadzenia instalacji.
Projekt w Serbii
Polska spółka zaprojektowała i wykonała prace wiertnicze w przekroczeniu rzeki Vielika Morava w Serbii w ramach budowy gazociągu łączącego system serbski z węgierskim. Początkowo przewiert zaprojektowano w technologii HDD, jednak po analizie geologicznej wybrano Direct Pipe (ze względu na problem z utrzymaniem stabilnego otworu).
Długość odcinka wynosiła 633 m, a średnica zewnętrzna rurociągu miała 1219 mm (48’’). Grubość ścianki to 21,1 mm. Izolację wykonano z 3LPE + Scar-guard. Prace trwały od grudnia 2019 r. do stycznia 2020 r., zrealizowano je w ciągu 18 dni. Średni dzienny postęp instalacji wynosił 1,4 m/godz., średnio dziennie układano 33,4 m rurociągu. Średnia siła instalacji wynosiła 880 kN, a maksymalna 1847 kN. Wykonano jedną lirę w trudnych warunkach geologicznych – grunt składał się w 80% ze żwiru i 20% z iłów.
Prace wiertnicze w Krempachach
Kolejny opisywany przez Marcina Firkowskiego projekt zrealizowano na budowie kanalizacji w Nowej Białej prowadzącej do oczyszczalni w Krempachach (gm. Nowy Targ) z przejściem pod rzeką Białką.
W tym przypadku wiercono odcinek o długości 430 m – długość od komory nadawczej w Krempachach do odbiorczej w Nowej Białej wynosiła około 340 m, a dodatkowy odcinek roboczy o długości 90 m wykonano, by wejść pod ziemię z odpowiednim kątem. Nieizolowany rurociąg miał średnicę zewnętrzną 1020 mm (40’’), grubość jego ścianki wynosiła 14,2 mm. Zadanie wykonano w kwietniu 2020 r. w ciągu 14 dni (trzy liry w gruncie złożonym ze żwiru i otoczaków). Pierwotnie instalacja miała powstać przy użyciu metody mikrotunelowania, jednak warunki geologiczne wymusiły zwiększenie średnicy do DN1600 i zdecydowano się na technologię DP.
Podczas prac wybudowano komorę rewizyjną pozwalającą na kontrolę osprzętu i wymianę tarczy głowicy. Urobek transportowano do urządzenia mielącego. Po demontażu urządzenia AVN800, wyciągnięto 340 mb instalacji wewnętrznej do komory nadawczej, a jednocześnie odbywało się pompowanie płuczki bentonitowo-cementowej. Likwidowany otwór zamknięto grodzicami. Rurociąg z odcinka roboczego został wyciągnięty, a pozostały po nim otwór wypełniono zaczynem cementowym.
Przeczytaj także: Konferencja „INŻYNIERIA Bezwykopowa” 2020 [relacja]
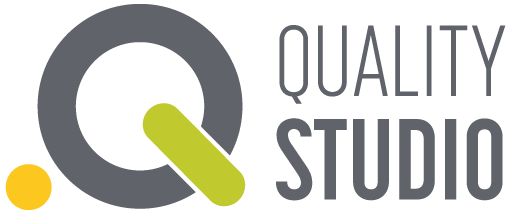
Foto, video, animacje 3D, VR
Twój partner w multimediach.
Sprawdź naszą ofertę!
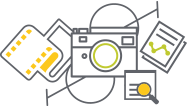
Aby dodać komentarz musisz być zalogowany. Przejdź do formularza logowania/rejestracji.