Z tekstu dowiesz się: jak zmieniały się wymogi jakościowe w odniesieniu do powłok laminatowych, jak rozwijał się rynek zabezpieczeń antykorozyjnych rur stalowych dla inwestycji bezwykopowych, jakie rozwiązania systemowe są stosowane w krajach europejskich.
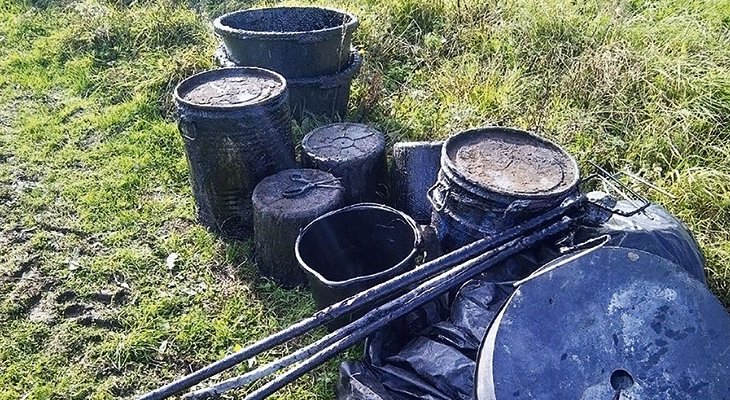
Pojęcie jakości towarzyszy ludzkości od zarania dziejów. Było ono stosowane już przez Platona, który używał go do określenia cech rzeczy. Arystoteles natomiast obok ilości, substancji, miejsca, czasu i tym podobnych sformułowań określających stan poszczególnych rzeczy, stawiał pojęcie jakości. Wyrażać ona miała określoność substancji cielesnej.
W wiekach późniejszych pojęcie „jakości” również było przedmiotem rozważań filozofów takich jak Kartezjusz, Emmanuel Kant, Georg Hegel. Chociaż pojęcie to uznane zostało przez filozofię za niedefiniowalne, nie przeszkodziło to w wykorzystywaniu tego terminu w szeregu innych dziedzin życia, w tym także (a może przede wszystkim), w gospodarce. Za „ojca” nowoczesnego podejścia do jakości uważa się natomiast Williama Edwardsa Deminga, którego poglądy oraz działania zapoczątkowały filozofię jakości znaną jako TQM – Total Quality Management. Według niego przedsiębiorstwa powinny mieć jeden cel – ciągłą poprawę jakości wytwarzanych produktów.
W tym kontekście rozwój izolacji antykorozyjnych nakładanych na rurach stalowych uznać należy na całkowicie zgodny z podejściem Deminga. Doskonale jest to widoczne, gdy prześledzi się zmiany w podejściu do jakości tych izolacji na przestrzeni ostatnich kilkudziesięciu lat. W segmencie izolacji stricte antykorozyjnych, stosowanych jako zabezpieczenie rur stalowych na gazociągach, technologiczna zmiana dokonała się na przełomie lat 80. i 90. ubiegłego stulecia, kiedy to izolacja bitumiczna została zastąpiona izolacją trójwarstwową. W izolacjach tych, warstwą odpowiedzialną za antykorozję jest warstwa epoksydowa, natomiast jej zabezpieczenie stanowi osłona polietylenowa lub polipropylenowa. Izolacje te były bezsprzecznie trwalsze i lepsze jakościowo od swoich poprzedniczek.
Zaimplementowanie tych wymagań stanowiło przełom w kontekście wytycznych dla laminatów oraz nadzoru nad ich jakością na polskim rynku
Natomiast na przestrzeni ostatnich kilkunastu lat można zaobserwować olbrzymie zmiany także w samym podejściu do izolacji trójwarstwowych. Analizując poszczególne parametry jakościowe tych powłok, zwrócić należy uwagę na ogromny wzrost wymagań jakościowych dla najistotniejszych cech wyrobu, np. dla parametru określającego wymaganą przyczepność izolacji do rury stalowej był to wzrost z 35 N/cm do 180 N/cm, a więc o ponad 500%. Podobna sytuacja miała miejsce, jeżeli chodzi o inne wymagania istotne dla jakości wyrobu, takie jak katodowy zanik przyczepności, wytrzymałość przy zrywaniu, udarność itp.
Wobec szybkiego rozwoju technologii bezwykopowych stosowanych podczas budowy gazociągów, pojawiło się zapotrzebowanie na nowy typ izolacji, która byłaby w stanie skutecznie zastąpić rurę ochronną, stosowaną zwykle dla takich technologii i jednocześnie właściwie zabezpieczyć izolację antykorozyjną na rurze przewodowej. Mimo znacznie krótszego okresu stosowania takich zabezpieczeń na rynku w stosunku do okresu stosowania izolacji stricte antykorozyjnych, również w tym segmencie doszło do znaczących zmian, zarówno w technologii produkcji, jak i podejścia do nadzoru nad wyrobem.
Pierwsze zabezpieczenia laminatowe, które były stosowane podczas budów gazociągów, wykonywane były ręcznie na placach budów, bez zachowania jakiegokolwiek reżimu technologicznego oraz badania parametrów jakościowych wytworzonej w ten sposób powłoki (fot. 1). Niosło to za sobą wiele zagrożeń, zarówno dla powodzenia całej inwestycji, jak i środowiska naturalnego.
W zakresie nadzoru jakościowego, była to także swoista terra incognita, ponieważ nawet parametry jakościowe dla takiego wyrobu nie były określone, poza oceną wizualną i grubością warstwy. Tak więc, tym bardziej trudno było w tym kontekście mówić o zapewnieniu jakości i jej deklarowaniu.
Jednym z pierwszych dokumentów, próbującym sformalizować oraz skodyfikować wymagania jakościowe dla laminatów stosowanych jako zabezpieczenie powłok antykorozyjnych rur na gazociągach, było sprawozdanie z badań przeprowadzone przez Instytut Górnictwa Naftowego i Gazownictwa w Krakowie (obecnie INiG) dla PGNiG S.A. w 1997 roku (fot. 2).
FOT. 2. | Sprawozdanie z badań laminatu IGNiG w Krakowie
Zawierało ono zbiór wymogów jakościowych dla powłoki laminatowej, określało sposób przeprowadzenia poszczególnych badań oraz finalnie przedstawiło wyniki tych badań na konkretnej powłoce.
Jednak dokument ten nie był szeroko stosowany jako punkt odniesienia dla jakości wyrobów funkcjonujących na rynku. Tak więc obszar jakości powłok laminatowych nadal pozostał nieusystematyzowany. Siłą rzeczy wobec braku wymagań jakościowych, również dokumenty potwierdzające jakość tych wyrobów albo nie istniały, albo wyrażały ogólne zapewnienie, że wyrób został wykonany „dobrze”.
Nie należy obawiać się korzystania ze sprawdzonych wzorców, wprowadzania ich na nasz rynek oraz rozwijania ich
Kolejna próba sformalizowania i dookreślenia wymagań jakościowych dla powłok laminatowych na polskim rynku została podjęta dopiero przez firmy Proma sp. z o.o. i Izostal S.A., w związku z rozpoczęciem produkcji laminatu w warunkach fabrycznych. Rozwiązanie to wprowadziło nie tylko zmianę jakościową w stosunku do dotychczas stosowanych laminatów nakładanych na rury na placu budowy, ale przede wszystkim zapoczątkowało proces parametryzowania i kontroli jakości laminatu jako zabezpieczenia rur.
W roku 2013 opracowany został przez Izostal S.A. „Raport z badań oraz wytyczne dotyczące powłoki laminatowej”. Był to dokument stanowiący quasi normę zakładową dla laminatu produkowanego w warunkach fabrycznych, z określeniem wymagań jakościowych oraz sposobu i częstotliwości badań. Jednocześnie dokument ten zawierał wyniki badań laminatu wyprodukowanego przez Proma sp. z o.o. (tab. 1–3). Dokument ten oraz jego drugie wydanie z roku 2016 stanowił standard w zakresie produkcyjnym i jakościowym, który musiał być spełniany podczas produkcji laminatu w Proma sp. z o.o.
Laminaty produkowane przez firmę Proma sp. z o.o. zgodnie z powyższymi wymaganiami spełniły oczekiwania rynku i w krótkim czasie stały się dominującym wyrobem w tym sektorze produktowym. Rozwiązanie zostało zaaprobowane przez rynek i w roku 2018 Gaz-System S.A. umieścił wymagania dla powłok laminatowych w dokumentacji technicznej dla dostaw inwestorskich. Wytyczne te w dużym stopniu bazowały na doświadczeniach zdobytych przez firmę Proma sp. z o.o. w trakcie kilku lat dostaw m.in. na inwestycje Gaz–System S.A.
Zaimplementowanie tych wymagań stanowiło przełom w kontekście wytycznych dla laminatów oraz nadzoru nad ich jakością na polskim rynku. Pozwoliło także na dokładne określenie dokumentów jakościowych potwierdzających jakość wyrobu i ustanowiło świadectwo odbioru 3.1. jako dokument podstawowy i powszechnie wymagany. W związku z tym, wprowadzony został wymóg niezależnej od produkcji kontroli jakości i obowiązkowego systemu nadzoru nad wyrobem i systemem badań. W roku 2019 na wniosek Proma sp. z o.o. Instytut Nafty i Gazu w Krakowie wystawił po raz pierwszy na polskim rynku Krajową Ocenę Zgodności (fot. 3) stanowiącą zbiór wymagań dla laminatów jako wyrobów budowlanych.
Dodatkowo, dokument ten, po wystawieniu przez producenta Krajowej Deklaracji Własności Użytkowych pozwalał na oznakowanie laminatu Promglass znakiem budowlanym.
FOT. 3. | Krajowa Ocena Techniczna wystawiona przez INiG w Krakowie dla laminatu Promglass
Zgodnie z ideą Deminga, Proma – mimo jednoznacznie pozytywnej opinii rynku dotyczącej jakości jej wyrobu – starała się cały czas podnosić jego jakość. W trakcie produkcji, badań, a przede wszystkim podczas dostaw rur w laminacie na place budów, odbywała się ciągła analiza nie tylko wyników własnych badań, ale głównie informacji zebranych od klientów i użytkowników jej wyrobu. Na tej podstawie na rynek został wprowadzony laminat Promglass SuperBond, który posiadał oprócz wcześniej uzyskanych wysokich parametrów jakościowych, wielkopowierzchniową przyczepność do powłoki antykorozyjnej oraz odporność na ścinanie materiału na poziomie ok. 2 MPa. Produkt ten był owocem współpracy działów B+R Proma sp. z o.o. Izostal S.A. oraz Wydziału Wiertnictwa Nafty i Gazu Akademii Górniczo-Hutniczej w Krakowie.
Parametry charakterystyczne dla laminatu Promglass SuperBond były niezwykle istotne podczas instalacji bezwykopowych, ponieważ eliminowały ryzyko delaminacji powłoki oraz jej zsunięcia się z rury po jej ewentualnym uszkodzeniu podczas instalacji. Zapewniało to całkowite bezpieczeństwo inwestycji w tym zakresie. W krótkim okresie po debiucie wyrobu na rynku, parametry te zostały zaimplementowane przez Gaz–System S.A. do specyfikacji jakościowych jako warunki wymagane dla laminatów.
O właściwym kierunku rozwoju powłok laminatowych Promglass świadczy liczba zrealizowanych w ostatniej dekadzie projektów nie tylko na rynku polskim, ale także na rynku europejskim. Najważniejsze z nich to: budowa gazociągu na Litwie – Klajpeda Terminal DN700, budowa gazociągu w/c Baltic Pipe na rurach DN1000 oraz pozostałych powiązanych inwestycji O.G.P. Gaz-System S.A. (Lwówek – Odolanów, Czeszów – Wierzchowice, Czeszów – Kiełczów, Zdzieszowice – Brzeg, Zdzieszowice – Kędzierzyn, Tworóg – Kędzierzyn, Strachocina – Granica RP, Strachocina – Pogórska Wola, Pogórska Wola – Tworzeń, Brzeg – Ziębice – Kiełczów, Dolna Odra II i wiele innych), projekty Czajka I i II, Serbia BELTRUB– Belgrade przejście pod rzeką Dunaj (South Stream), Bulgartransgaz EAD – przejście pod rzeką Lom i rzeką Yantra (South Stream). Łącznie dostarczono ponad 100 km rur w laminacie, z zakresu średnic DN700–1200, nie licząc rur innych gabarytów, dostarczanych na mniejsze projekty.
Dla rynku polskiego rozwiązaniem mogłoby być wprowadzenie dla dostawców sektora gazowego konieczności posiadania znaku np. Q INiG
Wszystkie zrealizowane projekty opierały się na laminacie produkowanym pod ścisłym nadzorem jakościowym służb wewnętrznych producenta, z wystawieniem świadectwa odbioru 3.1. przez niezależny dział jakości. Ponadto, dla projektów realizowanych np. dla Gaz-System S.A. oraz dla inwestycji takich jak Czajka czy South Straem, podczas całego cyklu produkcji i dostaw, zaangażowani byli inspektorzy pracujący na rzecz inwestora, którzy uczestnicząc w całym łańcuchu realizacyjnym, potwierdzali wymagany poziom jakości wyrobu. Tak realizowany nadzór nad produkcją oraz jakością wyrobu, pozwalał na zapewnienie bezpieczeństwa dla klienta i pomyślne zrealizowanie inwestycji.
Na postawie ostatnich kilkunastu lat rozwoju rynku zabezpieczeń antykorozyjnych rur stalowych dla inwestycji bezwykopowych, wydaje się, że zmiana technologiczna i jakościowa jaka dokonała się w tym sektorze, nie pozostawia już zbyt wiele miejsca na doskonalenie. Niemniej jednak zgodnie myślą Winstona Churchilla, że „sukces nigdy nie jest ostateczny” należałoby zastanowić się nad rozwiązaniem zapewniającym bezpieczeństwo nie tylko dla poszczególnych inwestycji w okresie ich realizacji, ale byłoby rozwiązaniem systemowym dla wszystkich dostaw wyrobów na polskim rynku. Rozwiązania takie funkcjonują z powodzeniem na rynku europejskim i są pozytywnym przykładem zabezpieczania przez poszczególne kraje swoich rynków pod względem jakości dostarczanych wyrobów. W kontekście tak odpowiedzialnych inwestycji jak inwestycje gazowe, wydaje się to podwójnie ważne.
Jako przykład takiego rozwiązania można przedstawić rolę organizacji C4Gas na rynku europejskim. Jest to organizacja audytorska, pracująca na rzecz największych podmiotów z krajów Europy Środkowej takich jak Fluxys, GRTGas, GRDF, Eustream, Terega, Engie i wielu innych. Jej zadaniem jest przeprowadzanie audytów i kwalifikacji potencjalnych dostawców wyrobów dla inwestorów zrzeszonych pod szyldem C4Gas. Proces kwalifikacji jest długotrwały i obejmuje wszystkie aspekty związane z produkcją oraz jakością wyrobu, poczynając od stosowanych przez producenta wyrobu surowców, a na sposobie dostawy kończąc. Zabezpiecza to inwestorów przed zakupem towarów niewiadomego pochodzenia, np. wyprodukowanego z niskojakościowych, tanich surowców. Finalnie, jedynie firmy posiadające certyfikat C4Gas (fot. 4) mogą dostarczać wyroby dla firm zrzeszonych w organizacji.
FOT. 4. | Certyfikat C4Gas wystawiony dla Izostal S.A.
Dla rynku polskiego analogicznym rozwiązaniem mogłoby być wprowadzenie dla dostawców sektora gazowego konieczności posiadania znaku np. Q INiG (fot. 5). Jest to propozycja Instytutu Nafty i Gazu w Krakowie, instytucji o niekwestionowanym autorytecie i doświadczeniu na rynku gazowym w Polsce. Polega ona na możliwości poddania certyfikacji określonej grupy wyrobów dostarczanych na rynek gazowy i uzyskania dla nich znaku jakości Q INiG.
FOT. 5. | Znak jakości Q INiG
Certyfikacja obejmowałaby następujące elementy:
– ocena wyrobu na zgodność z wymaganiami Kryteriów Technicznych opracowanych dla danej grupy wyrobów, w tym badania wyrobu w akredytowanych laboratoriach trzeciej strony,
– wstępna ocena warunków organizacyjno-technicznych w miejscu produkcji wyrobów,
– nadzór nad wydanym certyfikatem sprawowany poprzez coroczną kontrolę w miejscu produkcji wyrobów,
– kontrola wyrobów z rynku – raz w cyklu certyfikacji wg wymagań określonych w Kryteriach Technicznych.
– certyfikaty wydawane są na 3 lub 5 lat (5 lat jeżeli zakład posiada certyfikowany system zarządzania jakością na zgodność z ISO 9001) i przedłużane na analogiczne okresy.
Tak przeprowadzona certyfikacja pozwalałaby na zapewnienie bezpieczeństwa wyrobu oraz wyeliminowanie wyrobów o niskiej jakości. Novum, które nie było do tej pory szeroko stosowane nawet na rynku europejskim, czyli kontrola wyrobów z rynku, pozwalałaby wyeliminować nieuczciwych dostawców. Jest to rozwiązanie analogiczne do rozwiązań z powodzeniem stosowanych w innych krajach europejskich, które chcą zabezpieczyć swój rynek przez wyrobami niskiej jakości.
Górnolotne idee dotyczące ciągłego rozwoju nie muszą kończyć się w przestrzeni gabinetowej i głowach ich twórców
Rozwój rynku izolacji antykorozyjnych stosowanych przy instalacjach bezwykopowych jest przykładem, że górnolotne idee dotyczące ciągłego rozwoju nie muszą kończyć się w przestrzeni gabinetowej i głowach ich twórców. Na szczęście czasami udaje się je przełożyć i zastosować w realnych, choć często błotnistych i trudnych warunkach budów. Wzrost parametrów jakościowych oraz budowanie systemu nadzoru nad jakością wyrobu jest zadaniem trudnym, ale osiągalnym, gdy odpowiedzialność za wyrób jest ważnym elementem procesu decyzyjnego dotyczącego rozwoju organizacji. Podobnie powinno się myśleć o całym rynku, w szczególności o tak ważnym i strategicznym dla bezpieczeństwa kraju sektorze, jakim jest gazownictwo.
Wobec czego nie należy obawiać się korzystania ze sprawdzonych wzorców, wprowadzania ich na nasz rynek oraz rozwijania ich – ponieważ ten, kto się nie rozwija, zazwyczaj cofa i pozostaje w tyle za konkurencją.
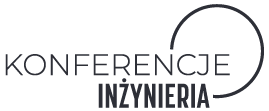
Konferencje Inżynieria
WIEDZA. BIZNES. ATRAKCJE
Sprawdź najbliższe wydarzenia
Aby dodać komentarz musisz być zalogowany. Przejdź do formularza logowania/rejestracji.