Podczas budowy gazociągów na obszarach o gęstej zabudowie, przy pokonywaniu przeszkód terenowych lub terenów przyrodniczo cennych, stosowane są zwykle metody bezwykopowe. Spośród tego typu technik najczęściej do realizacji przekroczeń wybierane są: przeciski hydrauliczne, mikrotunelowanie, horyzontalne wiercenia kierunkowe (HDD) oraz technologia Direct Pipe. Bezwykopowa instalacja rurociągów wymaga jednak właściwego ich zabezpieczenia.
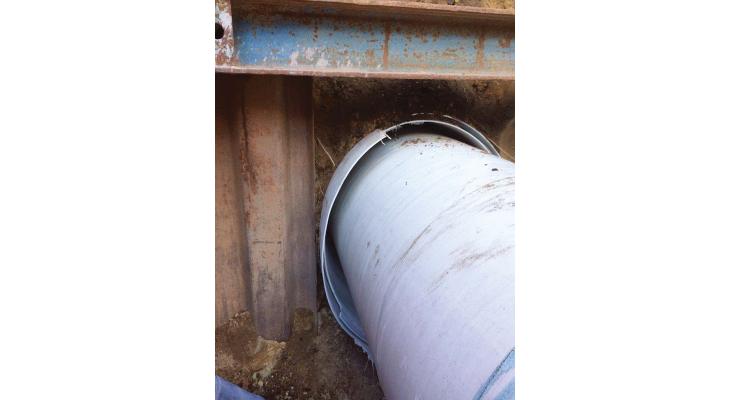
Budowa gazociągów metodami bezwykopowymi powinna być prowadzona ze ścisłym i charakterystycznym dla tego typu rozwiązań reżimem technologicznym, tak aby nie nastąpiło uszkodzenie powłok ochronnych rury przewodowej, tj. izolacji antykorozyjnej. Jest ona chroniona przez laminat szklano-żywiczny, który powinien charakteryzować się dużą odpornością na obciążenia mechaniczne oraz wysoką odpornością na ścinanie, co zabezpiecza powłokę przed zsuwaniem się z rury podczas wykonywania przewiertu. W związku z tym bardzo ważne jest właściwe wykonanie powłok laminatowych, poczynając od przygotowania powierzchni izolacji antykorozyjnej, a kończąc na nakładaniu laminatu w stałych powtarzalnych warunkach, ze ścisłym przestrzeganiem ustalonego reżimu technologicznego. Tak zaprojektowany proces gwarantuje wykonanie zabezpieczenia na wysokim poziomie jakościowym. Oczywiście, poziom ten musi być stale kontrolowany i nadzorowany poprzez prowadzenie badań jakościowych dla najważniejszych parametrów wyrobu.
Zastosowania laminatów jako zabezpieczenia izolacji antykorozyjnej
W kontekście zastosowania laminatów jako zabezpieczenia izolacji antykorozyjnej podczas stosowania metod bezwykopowych najistotniejszymi parametrami są:
- właściwa grubość warstwy;
- odporność na ścinanie, czyli przyleganie laminatu do powierzchni izolacji antykorozyjnej;
- elastyczność;
- twardość;
- wytrzymałość na zrywanie.
Zachowanie wartości tych parametrów na odpowiednio zaprojektowanym poziomie daje pewność, że przy dobrze wykonanym przejściu laminat spełni swoje zadanie i ochroni izolację antykorozyjną przed uszkodzeniami, a co za tym idzie, zapewni jej właściwą rezystywność.
Obecnie, podczas wykonywania przewiertów HDD (ang. Horizontal Directional Drilling) lub Direct Pipe, rezystancja przejścia rco powinna być zachowana na poziomie 108Ωm2, co jest wymaganiem równym progowemu wymogowi dla fabrycznej izolacji antykorozyjnej, badanej bezpośrednio po jej nałożeniu w warunkach zakładu produkcyjnego, bez narażania jej na uszkodzenia mechaniczne wynikające z transportu oraz przejścia przez otwór wiertniczy. Aby zapewnić tak wysokie parametry w warunkach budowy, laminat zabezpieczający izolację musi być najwyższej jakości.
Firma Proma sp. z o.o., jako producent laminatów szklano-żywicznych nakładanych na rury przewodowe w izolacji antykorozyjnej, z powodzeniem stosuje technologię, która pozwala zapewnić odpowiednią jakość jej wyrobów, a co za tym idzie, zagwarantować bezpieczeństwo rur instalowanych bezwykopowo. Świadectwem dobrze wykonanej pracy są już zrealizowane metodami bezwykopowymi przejścia, gdzie rury pokryto laminatem typu Promglass. W tab. 1 przedstawiono, na których odcinkach nowo budowanych gazociągów zastosowano takie rozwiązanie.
Wszystkie te wymagające realizacje, co trzeba podkreślić, zakończyły się sukcesem. Izolacja antykorozyjna w tych przypadkach posiadała rezystancję przejścia zawsze powyżej 108Ωm2. Jednakże inwestycje tego typu niejako z definicji charakteryzują się dużym stopniem trudności i ryzyka w każdym aspekcie realizacyjnym, a każdy popełniony błąd niesie ze sobą konieczność ponoszenia ogromnych, dodatkowych nakładów finansowych. W związku z tym intencją producenta laminatu jest zagwarantowanie, że zarówno wykonawca, jak i inwestor będzie miał zapewnioną najwyższą jakość wyrobu, co pozwoli wyeliminować większość zagrożeń.
Przyczepność chemiczna laminatu
Jednym z większych zagrożeń dotyczących zabezpieczenia rur instalowanych bezwykopowo jest brak przyczepności chemicznej laminatu do izolacji antykorozyjnej. Oferowane na rynku produkty posiadają większą lub mniejszą odporność na ścinanie. Wynika ona wyłącznie ze skurczu obwodowego nałożonego laminatu oraz mechanicznego przygotowania powierzchni izolacji antykorozyjnej przed rozpoczęciem nakładania powłoki. Daje to możliwość utrzymania jej na rurze do momentu ścięcia żywicy zagnieżdżonej w porowato rozwiniętej powierzchni izolacji antykorozyjnej. Dobrze przygotowana powierzchnia i nałożenie laminatu w stałych warunkach, z utrzymaniem właściwego reżimu technologicznego i kontroli, gwarantuje wykonanie powłoki spełniającej wymagania wytrzymałości na ścinanie na poziomie 50 N/cm2.
Trzeba jednak zauważyć, że wszystkie laminaty oferowane do tej pory na rynku europejskim, które mają wspomniane parametry (oczywiście pominąć należy laminaty wykonywane na placu budowy, bez reżimu technologicznego oraz bez jakiegokolwiek przygotowania powierzchni izolacji antykorozyjnej), posiadają je tylko do momentu zachowania ciągłości warstwy laminatowej. Po jej przerwaniu, co może się zdarzyć i niejednokrotnie zdarza się podczas instalowania rurociągów, laminatowa warstwa ochronna traci większość ze swych parametrów i na skutek oporów w otworze wiertniczym może zacząć zsuwać się z rury, a nawet może być przyczyną zablokowania otworu laminatem (fot. 1).
W związku z tym Proma sp. z o.o. we współpracy z Izostal S.A. rozpoczęła prace nad powłoką laminatową, która będzie posiadała wielkopowierzchniową przyczepność chemiczną do odpowiednio przygotowanej powierzchni izolacji antykorozyjnej. Powłoka taka w założeniu ma posiadać wszystkie wysokie parametry wytrzymałościowe standardowej powłoki Promglass, a dodatkowo będzie znacznie bardziej odporna na ścinanie oraz będzie posiadała przyczepność chemiczną na każdym centymetrze kwadratowym powłoki. Po spełnieniu tych warunków upodobni się do powłoki antykorozyjnej, która w temperaturze do 80°C jest praktycznie nieusuwalna. Zapewni to w praktyce brak możliwości zsunięcia się jej z rury, nawet po jej miejscowym rozerwaniu. W efekcie wyeliminowane zostaną przypadki uszkadzania na dużych powierzchniach nieosłoniętej powłoki antykorozyjnej oraz blokowania otworów laminatem.
RYS. 1. Schemat badania wytrzymałości laminatu na ścinanie
W celu uzyskania odpowiedzi na pytanie, czy badania nad wyrobem prowadzone są we właściwym kierunku, przeprowadzono testy odporności laminatu na ścinanie oraz jego przyczepności do izolacji antykorozyjnej. Wytrzymałość badana była zgodnie ze standardem DVGW GW 340. Podczas takiego badania na próbkę działa siła skierowana równolegle do osi rury, co symuluje siły działające na laminat w otworze wiertniczym (rys. 1).
Z rezultatów badań wynika, że na próbkach laboratoryjnych przygotowanych w sposób symulujący różne wykonania laminatu, wartość wytrzymałości na ścinanie w znacznym stopniu się różni. I tak:
- nałożenie laminatu na powierzchnię izolacji antykorozyjnej bez jej przygotowania (symuluje wykonanie polowe) – wytrzymałość na ścinanie to około 5 N/cm2;
- nałożenie laminatu na powierzchnię izolacji antykorozyjnej przygotowaną mechanicznie (symuluje wykonanie fabryczne) – wytrzymałość na ścinanie to około
- 60 N/cm2;
- nałożenie laminatu na specjalnie przygotowaną powierzchnię izolacji antykorozyjnej (wykonanie innowacyjne, z przyczepnością chemiczną) – wytrzymałość na ścinanie to około 200 N/cm2.
Przedstawione wyniki pokazują jednoznacznie, jak ogromny wpływ ma zastosowanie innowacyjnej technologii na jeden z najistotniejszych parametrów laminatu, tj. na wytrzymałość na ścinanie, co wydaje się w pełni potwierdzać założenia rozwojowe projektu.
Kolejnym badanym, a niezwykle istotnym parametrem laminatu, jest jego przyczepność do powierzchni izolacji antykorozyjnej. Jest to parametr nieosiągalny dla laminatów oferowanych w tej chwili na rynku. Innowacyjne rozwiązanie, nad którym pracuje Proma sp. z o.o., pozwoli zbliżyć się parametrami przyczepności wielkopowierzchniowej laminatu do tej, jaką posiada izolacja antykorozyjna do powierzchni rury stalowej i zapewnić jego nienaruszalność podczas instalacji bezwykopowej. W związku z tym, aby potwierdzić przyjęte założenia, na obwodzie rury (na osiach umieszczonych prostopadle względem siebie) wycięte zostały w laminacie cztery kwadraty o boku 2 cm. Wektor siły odrywającej został skierowany prostopadle do osi rury (rys. 2), a prędkość odrywania wynosiła 10 mm/min.
RYS. 2. Przygotowanie próbki do badania przyczepności
Podobnie jak w przypadku ścinania, wyniki zasadniczo różnią się dla poszczególnych sposobów wykonania laminatu:
- nałożenie laminatu na powierzchnię izolacji antykorozyjnej bez jej przygotowania (symuluje wykonanie polowe) – przyczepność wynosi 0 N/cm2 dla wszystkich czterech próbek;
- nałożenie laminatu na powierzchnię izolacji antykorozyjnej przygotowaną mechanicznie (symuluje wykonanie fabryczne) – przyczepność to około 80 N/cm2 dla dwóch próbek i 0 N/cm2 dla dwóch pozostałych;
- nałożenie laminatu na specjalnie przygotowaną powierzchnię izolacji antykorozyjnej (wykonanie innowacyjne, z przyczepnością chemiczną) – przyczepność powyżej 200 N/cm2 dla wszystkich czterech próbek.
Na podstawie przedstawionych wyników można stwierdzić, że laminat nałożony metodą polową, bez przygotowania mechanicznego izolacji antykorozyjnej, nie posiada do niej żadnej przyczepności. Przy wykonaniu fabrycznym niewielka przyczepność występuje miejscowo i jest wynikiem wnikania żywicy w utworzone pory izolacji antykorozyjnej po jej mechanicznym przygotowaniu. Natomiast przy innowacyjnym przygotowaniu powierzchni izolacji przyczepność występuje w każdym jej punkcie i jest bardzo wysoka.
Podsumowanie
Reasumując, z punktu widzenia nie tylko wykonawcy laminatu, ale przede wszystkim wykonawców i inwestorów projektów gazowych, wyniki uzyskane podczas wstępnych prac laboratoryjnych dają szansę na rozwinięcie i wytworzenie wyrobu, który pozwoli na uniknięcie wielu istotnych zagrożeń podczas realizacji inwestycji z sektora gazowego metodami bezwykopowymi. Może to być krok w kierunku uzyskania produktu, który całkowicie zaspokoi oczekiwania branży gazowniczej w stosunku do zabezpieczania izolacji antykorozyjnej podczas przewiertów i przecisków.
Oczywiście od prac laboratoryjnych, które nie są jeszcze w pełni zakończone, do przygotowania produkcji na skalę przemysłową jeszcze daleka droga, jednak patrząc z perspektywy dotychczasowych wyników i doświadczeń, wydaje się, że jest to właściwy kierunek rozwoju wyrobu.
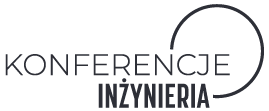
Konferencje Inżynieria
WIEDZA. BIZNES. ATRAKCJE
Sprawdź najbliższe wydarzenia
Aby dodać komentarz musisz być zalogowany. Przejdź do formularza logowania/rejestracji.